In the process of using cartons, there are two main problems:
1. Fat bag or bulging bag 2. Damaged carton
Topic 1
One, fat bag or drum bag reason
1. Improper choice of flute type
2. The impact of stacking finished shovels
3. Did not determine the size of the box height
Two, Measures to solve the fat or bulging cartons
1. Determine the corrugated type of the carton as the appropriate type
Among Type A, Type C, and Type B corrugations, Type B has the lowest corrugation height, and although the vertical pressure resistance is poor, the plane pressure is the best. After the carton adopts B-type corrugation, although the compressive strength of the empty carton will decrease, the contents are self-supporting and can bear part of the stacking weight when stacked, so the stacking effect of the product is also good. In actual production, different flute types can be selected according to specific conditions.
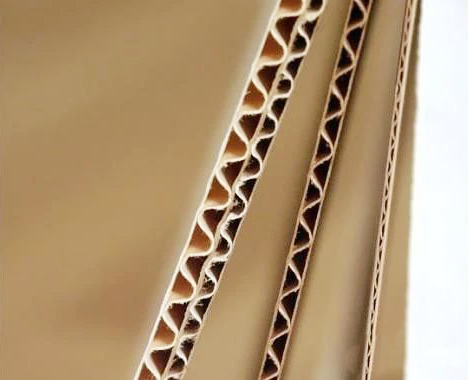
2. Improve the stacking conditions of products in the warehouse
If the warehouse location allows, try not to stack two shovels high. If it is necessary to stack two shovels high, in order to prevent the concentration of the load when the finished products are stacked, a corrugated cardboard can be sandwiched in the middle of the stack or a flat shovel can be used.
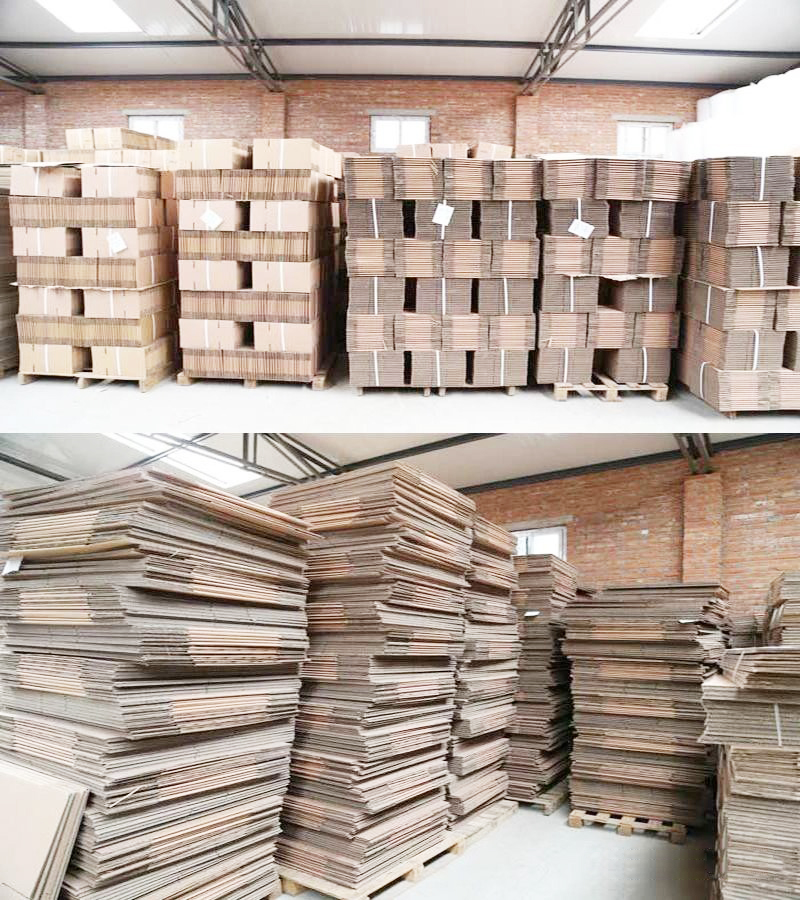
3. Determine the exact carton size
In order to reduce fat bags or bulges and reflect a good stacking effect, we set the carton height to be the same as the bottle height, especially for carbonated beverage cartons and pure water tanks with relatively high carton heights.
Topic 2
One, the main factor of carton damage
1. The size design of the carton is unreasonable
2. The thickness of corrugated cardboard does not meet the requirements
3. Corrugated deformation of cartons
4. Unreasonable design of the cardboard layers of the carton
5. The bonding strength of the carton is poor
6. The printing design of the carton is unreasonable
7. The regulations on the paper used in the carton are unreasonable and the paper used does not meet the requirements
8. Effects of transport
9. Poor management of seller's warehouse
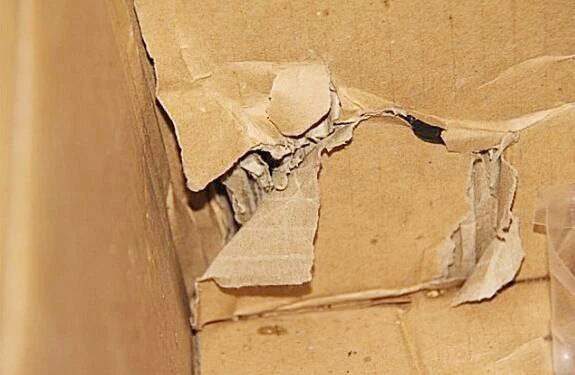
Two, specific measures to solve carton damage
1. Design reasonable carton size
When designing cartons, in addition to considering how to use the most economical materials under a certain volume, you should also consider the restrictions on the size and weight of a single carton in the market circulation link, sales habits, ergonomic principles, and the convenience and rationality of the internal arrangement of products. sex etc. According to the principle of ergonomics, the appropriate size of the carton will not cause fatigue and injury to the human body. Overweight carton packaging will affect transportation efficiency and increase the probability of damage. According to international trade practice, the weight limit of a carton is 20kg. In actual sales, for the same product, different packaging methods have different popularity in the market. Therefore, when designing a carton, try to determine the size of the package according to sales habits.
Therefore, in the process of carton design, various factors should be considered comprehensively, and the compressive strength of the carton should be improved without increasing the cost and affecting the packaging effect. And after fully understanding the characteristics of the contents, determine the reasonable size of the carton.
2. Corrugated cardboard reaches the specified thickness
The thickness of corrugated cardboard has a great influence on the compressive strength of the carton. During the production process, the corrugating rollers are severely worn, resulting in a decrease in the thickness of the corrugated cardboard, and a decrease in the compressive strength of the carton, resulting in an increase in the breakage rate of the carton.
3. Reduce the deformation of corrugated
First of all, it is necessary to control the quality of base paper, especially the physical indicators such as ring crush strength and moisture of corrugated medium paper. Secondly, the corrugated cardboard process is studied to change the corrugated deformation caused by factors such as the wear of the corrugated rollers and the insufficient pressure between the corrugated rollers. Third, improve the carton manufacturing process, adjust the gap between the paper feed rollers of the carton machine, and change the carton printing to flexographic printing to reduce corrugated deformation. At the same time, we should also pay attention to the transportation of cartons, and try to use vans to transport cartons to reduce corrugated deformation caused by bundling of oilcloths and ropes and trampling of stevedores.
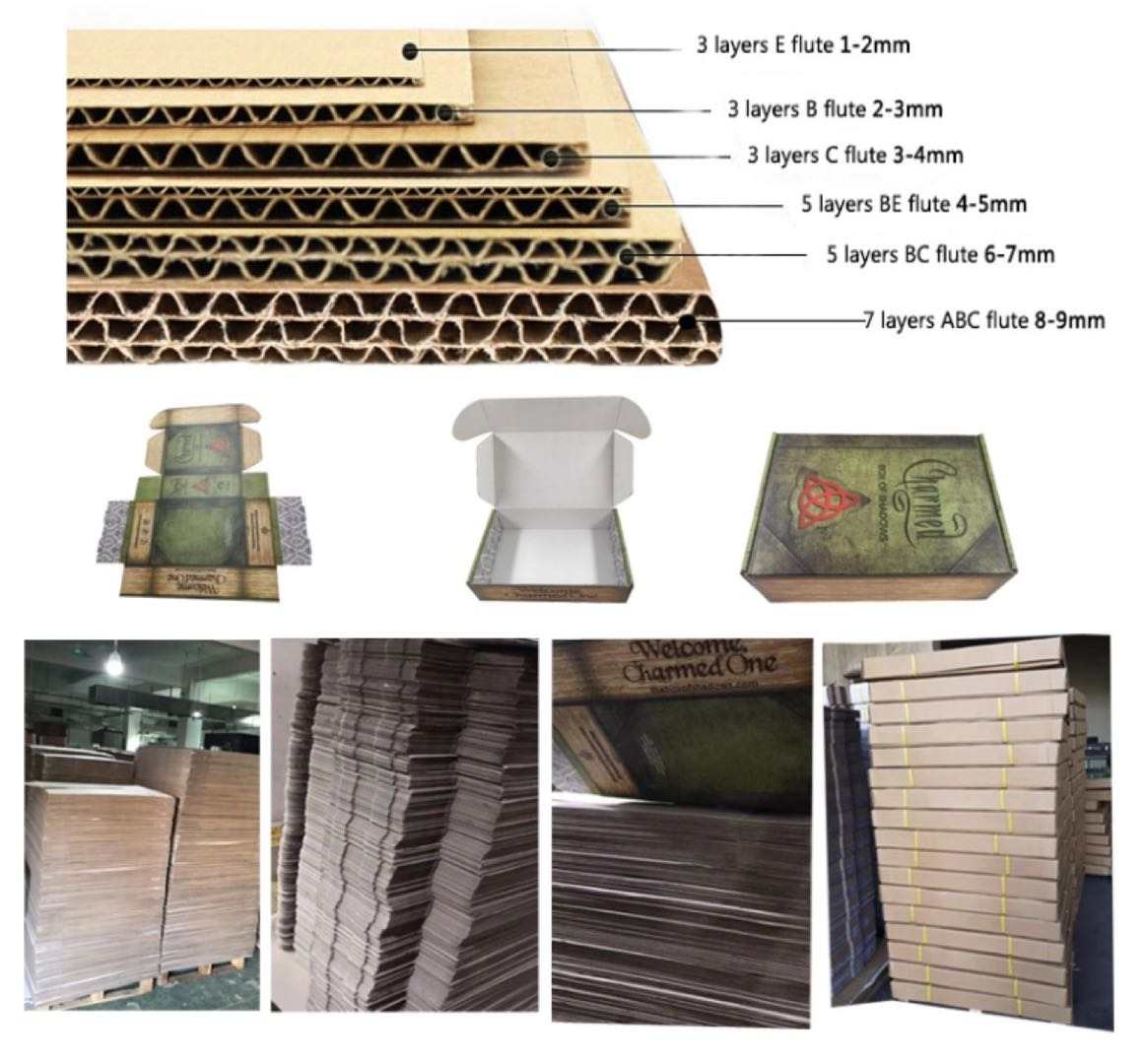
4. Design the right number of layers of corrugated cardboard
Corrugated cardboard can be divided into single layer, three layers, five layers and seven layers according to the number of layers of the material. As the number of layers increases, it has higher compressive strength and stacking strength. Therefore, it can be selected according to the characteristics of the product, environmental parameters and consumer requirements.
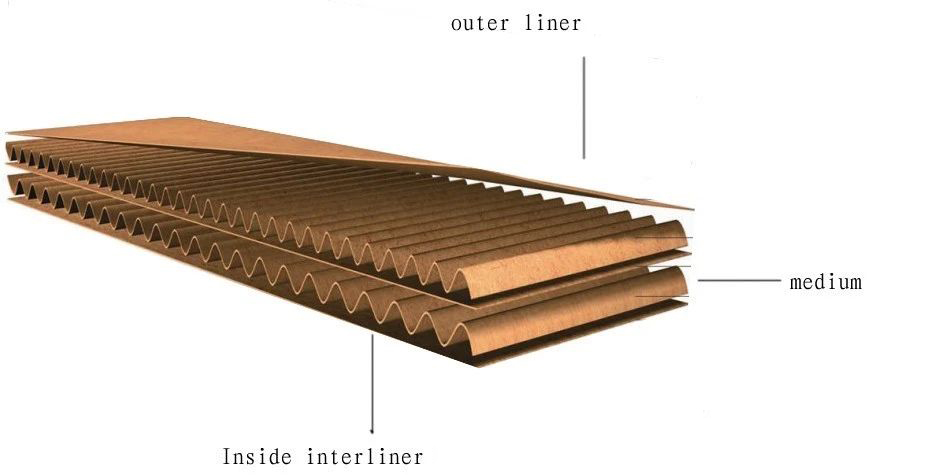
5. Strengthen the control of the peel strength of corrugated boxes
The bonding strength between the corrugated core paper of the carton and the face paper or inner paper can be controlled by testing instruments. If the peel strength does not meet the standard requirements, find out the reason. Suppliers are required to strengthen the inspection of carton raw materials, and the tightness and moisture content of the paper must meet the relevant national standards. And by improving the quality of the adhesive, improving equipment, etc. to achieve the peel strength required by the national standard.
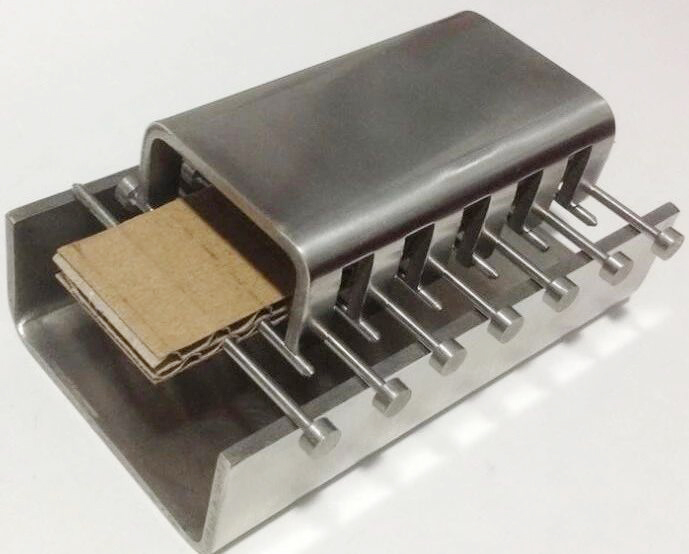
6. Reasonable design of carton pattern
Cartons should try to avoid full-page printing and horizontal strip printing, especially horizontal printing in the center of the box surface, because its function is the same as that of the horizontal pressure line, and the printing pressure will crush the corrugated. When printing the design on the box surface of the carton, it is necessary to minimize the number of color registers. Generally, after single-color printing, the compressive strength of the carton is reduced by 6%-12%, while after three-color printing, it will be reduced by 17%-20%.
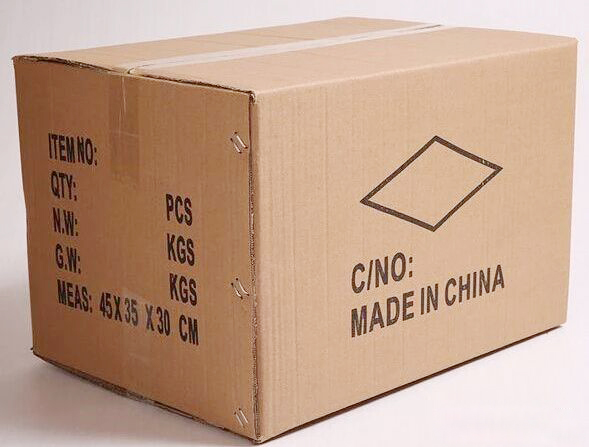
7. Determine the appropriate paper regulations
In the specific design process of carton paper, appropriate base paper should be properly selected. The quality of raw materials is the main factor determining the compressive strength of corrugated cartons. Usually, the compressive strength of corrugated boxes is directly proportional to the quantitative, tightness, stiffness, transverse ring compressive strength and other indicators of the base paper; it is inversely proportional to the moisture content. In addition, the influence of the appearance quality of the base paper on the compressive strength of the carton cannot be ignored.
Therefore, to ensure sufficient compressive strength, first of all, high-quality raw materials must be selected. However, when designing the paper used for cartons, do not blindly increase the weight and grade of the paper and increase the total weight of the cardboard. In fact, the compressive strength of corrugated boxes depends on the combined effect of the ring compressive strength of the face paper and corrugated medium paper. The corrugated medium has a greater impact on the strength, so no matter in terms of strength or economical considerations, the effect of improving the performance of the corrugated medium grade is better than that of improving the surface paper grade, and it is much more economical. It is possible to control the paper used in cartons by going to the supplier for on-site inspection, taking samples of the base paper, and measuring a series of indicators of the base paper to prevent cutting corners and shoddy.
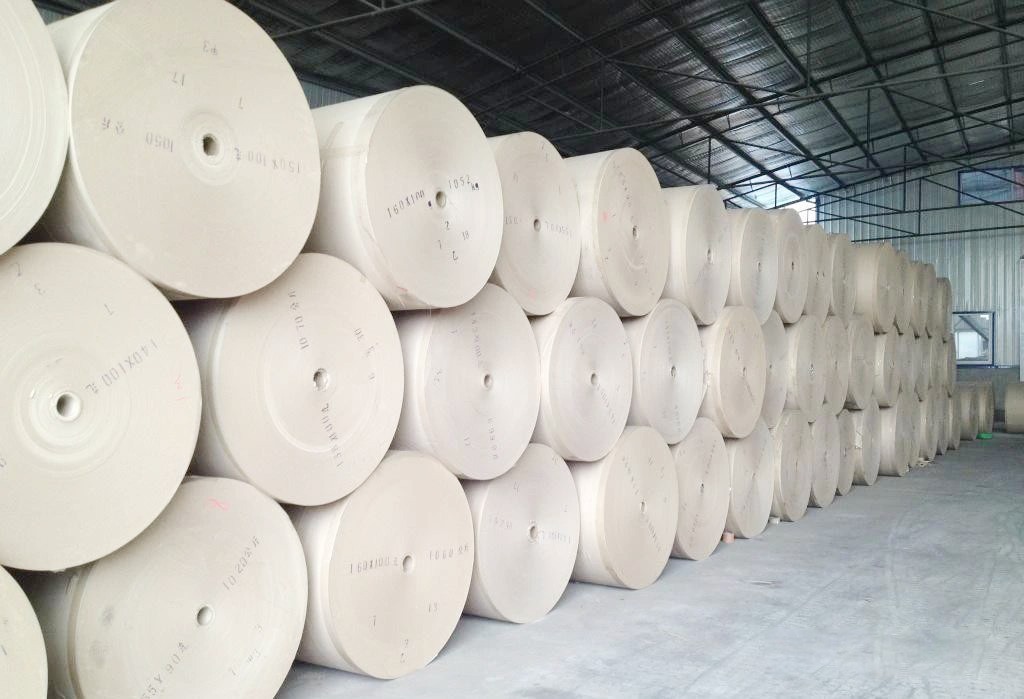
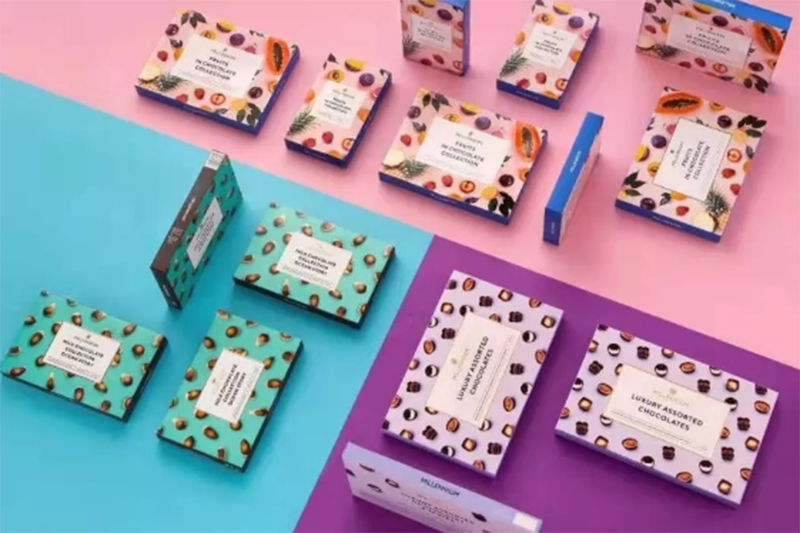
8. Improved shipping
Reduce the frequency of commodity transportation and handling, adopt the method of nearby delivery, and improve the handling method (it is recommended to use shovel handling); educate the porters, etc., improve their quality awareness, and prevent rough loading and unloading; pay attention to rain and moisture when loading and transporting , the binding cannot be too tight, etc.
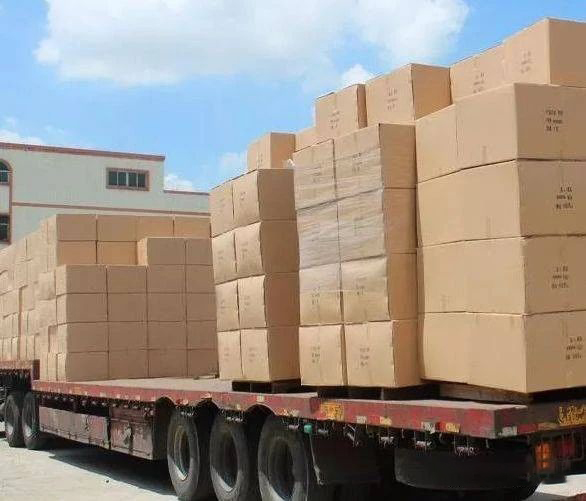
9. Strengthen the management of dealer warehouses
The first-in-first-out principle should be followed for the products sold, the number of stacked layers should not be too high, the warehouse should not be too humid, and should be kept dry and ventilated.
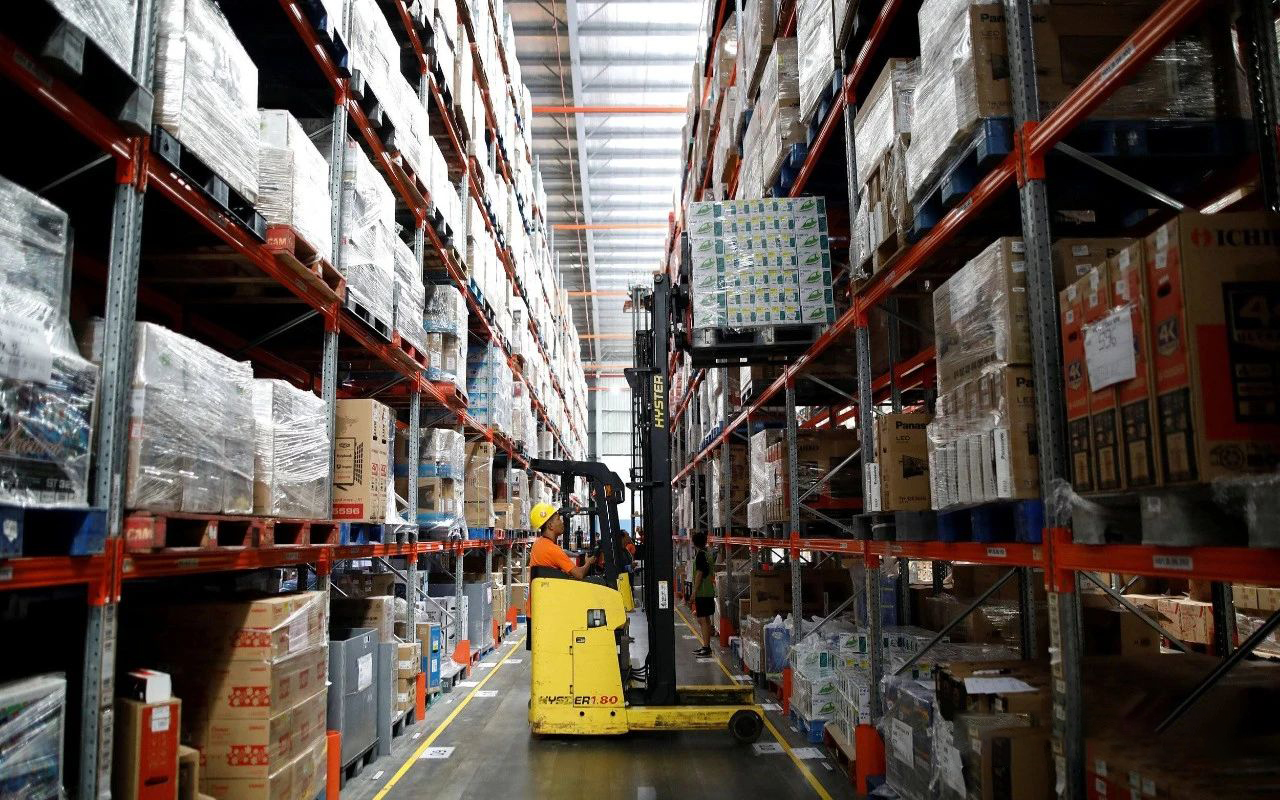
Post time: Feb-07-2023