The lining grids of various packages made of corrugated cardboard can be designed in various styles according to the needs of the packaged objects. They can be inserted and folded into various shapes to meet the needs of protecting the goods. Corrugated cardboard lining accessories are an excellent choice for packaging and are often the first choice for accessories.
Accessories made of corrugated cardboard have the advantages of simple processing technology, light weight, and low cost. They can also reuse the leftover corners of other packaging products, which saves resources and reduces waste. These accessories will not pollute the environment during use and are easy to recycle, so they are widely used.
Internationally, these accessories are designated by the Type 09 designation. My country's national standard, GB/6543-2008, also provides the styles and codes of various accessories in the standard informative annexes.
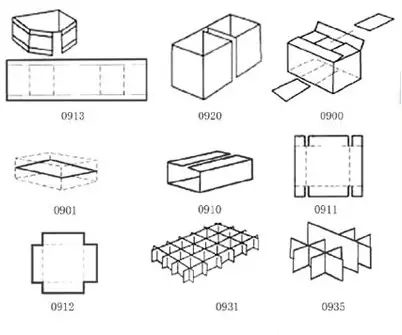
▲Various styles of accessories
What physical properties should accessories made of corrugated cardboard have to meet the needs of packaging? This is a question that designers need to study and explore.
Corrugated cardboard accessories are mostly formed in the form of inserts or folded. In the package, they mainly play the role of barrier and filling.
First of all, let's analyze the force of these accessories in the package during storage and transportation. During transportation, when the package is subjected to an external force from the horizontal direction (X direction), such as a sudden brake, the internal parts will move forward in the horizontal direction due to inertia, and along the direction of movement, the front and rear attachment walls of the part will be generated. impact.
Since the material of the accessory wall is corrugated cardboard, it has a certain cushioning performance, which will reduce the harm caused by the impact force. At the same time, the part may have friction with the left and right accessory walls or the packaging at the top and bottom of the part. Due to the friction, the movement of the contents will be quickly slowed down or prevented (the same is true for the Z direction).
If the package is subjected to vertical (Y direction) vibration and impact, the internal parts will move in the up and down direction, which will impact the top and bottom of the packaging box of the parts. Similarly, due to the top and bottom packaging materials with certain cushioning properties, It will also play a certain role in reducing impact hazards. And it may also generate friction with the four walls of the accessory, preventing or reducing the up and down movement of the contents.
Except for special needs, the accessories do not play a supporting role in the entire package. Therefore, in general, during the stacking process, the accessories only play a role of separation and do not make much contribution to other aspects.
Let’s analyze the possibility of damage to accessories and packaging containers during storage and transportation. Since these accessories fill most of the space of the package, the contents of the package do not have much room for movement and can touch the wall of the accessory. , due to the effect of friction, the movement of the contents is prevented. Therefore, the parts of the accessories affected by the impact and the impacted part of the package will not be greatly damaged. Since these accessories are protected by packaging containers, they will not be damaged during normal storage.
The above analysis requires that the accessories have a certain cushioning performance and a certain friction coefficient. Due to the requirements of processing and use, the accessories should also have certain folding resistance. In the process of storage and transportation, the accessories are generally not subject to pressure, and the accessories that do not have a supporting role do not have high requirements for the compression resistance of the edge of the corrugated cardboard. Therefore, except for special needs, the national standard GB/6543-2008 S- 2. Or the edge pressure and burst resistance indicators in B-2.1 can meet the needs.
A good packaging design means that the various performances of the packaging product are just enough to protect the product from manufacturing and distribution to the hands of customers. The pursuit of excessive packaging will cause a waste of resources, which is not worth advocating. How to achieve the maximum between improving product quality and saving resources, reasonable raw material ratio, reasonable design and process, and reasonable use are the methods to solve the problem. Based on the experience and experience in the work, the author puts forward some countermeasures for communication and discussion.
Countermeasure one:
Choose a reasonable ratio of raw materials
Ordinary accessories made of corrugated cardboard do not have high requirements for edge pressure and burst resistance. You should try to choose C, D, and E-grade base paper. As long as the performance meets the needs, do not pursue excessive strength and try not to use sizing. base paper. Because the sizing base paper has high strength, but the cushioning performance is not good, and the surface of the paper becomes smooth due to sizing, and the coefficient of friction is reduced, which reduces the packaging effect on the contrary. Therefore, high-quality cardboard is not necessarily suitable for making accessories.
1. Plug-in format accessories
It mainly acts as a barrier. The raw material does not need to be too hard or too strong. On the contrary, a softer material is more conducive to its cushioning effect. Rougher materials have a higher coefficient of friction, which is beneficial to improve the protection of the contents. Plug-in format accessories are mostly in an upright state when used, and require a certain degree of stiffness. In the ratio of raw materials, in addition to choosing base paper without sizing, thicker base paper should also be considered for the same quality level of base paper. In order not to increase the weight, you can choose a base paper with a smaller tightness, so that the accessories can maintain a good upright state, which is conducive to the operation and packaging effect during packaging, and the looser base paper has better cushioning performance than the tight base paper, which is more conducive to packaging. storage and transportation.
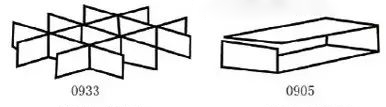
2. Folding accessories
When choosing the ratio of raw materials, not only the above requirements must be met, but also due to the folding requirements in production and use, the base paper needs to have a certain folding resistance, and try to choose a face paper with a slightly higher folding resistance for the ratio. Try not to choose sizing base paper, especially do not use sizing base paper for corrugation, because sizing corrugation will increase the possibility of surface paper breakage.
Nowadays, there are many types of base paper, and there is a wide range of options to choose from. As long as you choose a reasonable ratio carefully, you will find great potential in improving product quality and saving resources.

▲Various styles of accessories
Countermeasure two:
Choose a reasonable indentation process
From the above analysis, if the folding resistance of the accessories made of corrugated cardboard is not good, it will cause breakage at the fold line during processing or use. Choosing a reasonable indentation process is one of the countermeasures to reduce breakage.
Appropriately increase the width of the indentation line, and the wider indentation line, in the process of indentation, due to the increase of the compressed area, the stress at the indentation is dispersed, thereby reducing the possibility of fracture at the indentation . Using a softer, less sharp creasing tool, such as a plastic one, can also reduce breakage at the creasing line.
If the creases of these accessories are folded in the same direction, the touch line process can be used. In this way, during processing, the material on both sides of the indentation line has a certain pre-stretch, which can also play a certain role in reducing fracture.
Countermeasure three:
choose a reasonable design
When the supporting function of accessories is not considered, it is a good way to improve the folding resistance by choosing indentation in the same direction as possible.
For the corrugated cardboard manufactured by the production line and single-facer machine, the direction of corrugation is parallel to the transverse direction of the base paper. Choose the indentation in the same direction as the corrugation. When processing and using, it is to fold the base paper in the longitudinal direction.
One is that the longitudinal folding resistance of the base paper is higher than the transverse folding resistance, which will reduce the breakage at the creasing line.
The second is to indent in a direction parallel to the corrugated direction. The stretching effect of the materials on both sides of the indentation is in the longitudinal direction of the base paper. Because the longitudinal breaking force of the base paper is higher than the transverse breaking force, the tension around the fold is reduced. fracture. In this way, the same raw material, through reasonable design, can play a very different role.
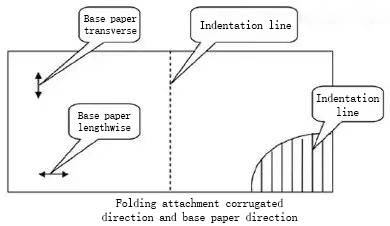
Countermeasure four:
Choose a reasonable method of use
The accessories made of corrugated cardboard have a certain range of strength due to the properties of the raw materials. When using the accessories, do not apply excessive external force to prevent them from breaking. When using a folding accessory, it must not be folded 180° at once.
Because paper products are hydrophilic materials, the environmental humidity during use and the moisture content of accessory materials are also factors that affect the fracture of accessories. The moisture content of corrugated cardboard is generally between (7% and 12%). In terms of effect, it is more appropriate. The environment or material is too dry, which will increase the possibility of cardboard breakage. But this is not to say that the more wet the better, too wet will make the contents damp. Of course, the use is generally carried out in the natural environment, so the user should take appropriate measures according to the environment and material conditions.
These inserts and folding accessories seem insignificant and have not attracted much attention. After quality problems occur, the quantitative improvement of base paper is often used to achieve the purpose of improving quality. Some replace the base paper with high-strength and sizing base paper, which may solve problems such as breakage, but reduce other performances. This will not only fail to solve the fundamental problem, but will also increase costs and cause waste.
The accessories in the package are used in a large amount, as long as some small improvements are made to it, the original resources will be more effective.
Post time: Mar-03-2023