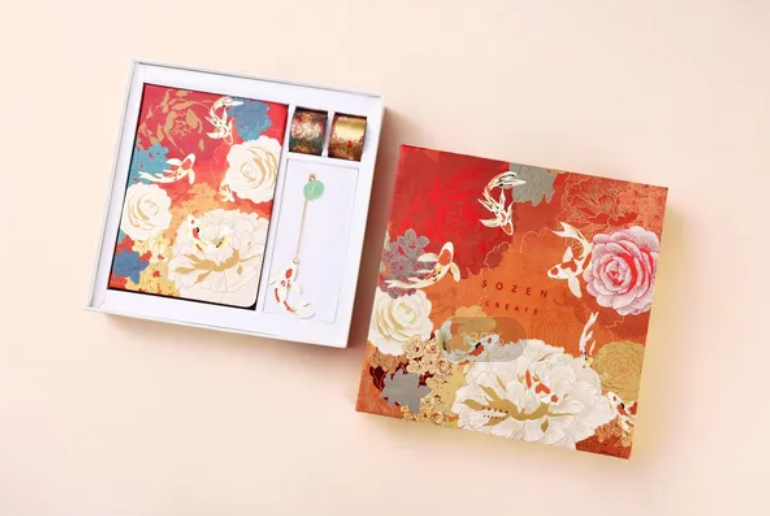
As the name suggests, packaging boxes are used to package products. Beautiful packaging boxes always leave a lasting impression, but have you ever wondered what materials are used to create these exquisite boxes?
Packaging boxes can be classified according to the materials they are made from, including paper, metal, wood, cloth, leather, acrylic, corrugated cardboard, PVC, and more. Among them, paper boxes are the most commonly used and can be divided into two main categories: linerboard and corrugated board.
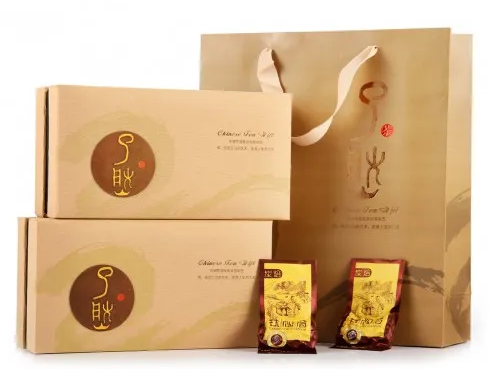
Paperboard boxes are made from a variety of materials, such as kraft paper, coated paper, and ivory board. Linerboard, also known as the surface paper, is the outer layer of the paperboard, while corrugated board, also known as the fluted paper, is the inner layer. The combination of the two provides the necessary strength and durability for the packaging box. Metal boxes, on the other hand, are commonly made from tinplate or aluminum. Tinplate boxes are often used for food packaging due to their excellent preservation properties, while aluminum boxes are lightweight and durable, making them suitable for various products. Wooden boxes are known for their durability and strength, and are often used for high-end products such as jewelry or watches. They can be made from various types of wood, including oak, pine, and cedar, depending on the desired appearance and function of the box. Cloth and leather boxes are often used for luxury products such as perfumes or cosmetics. They provide a soft and elegant touch to the packaging and can be customized with various patterns and textures. Acrylic boxes are transparent and often used for display purposes, such as showcasing jewelry or collectibles. They are lightweight and shatter-resistant, making them a popular choice for retail packaging. Corrugated cardboard boxes are made from a fluted layer sandwiched between two linerboards. They are commonly used for shipping and transportation due to their durability and strength. PVC boxes are lightweight and waterproof, making them a popular choice for packaging electronic products or other items that require protection from moisture. In conclusion, choosing the right packaging box material is crucial in ensuring the safety and presentation of your product. Each material has its own unique properties and characteristics, and it’s important to consider factors such as product type, transportation method, and customer preference when selecting the appropriate material for your packaging box.
Today, let’s learn about the commonly used surface paper and corrugated paper materials in packaging boxes!
01
01 Surface Paper
Commonly used paperboards in surface paperboard include: copperplate paper, grey board paper, and special paper.
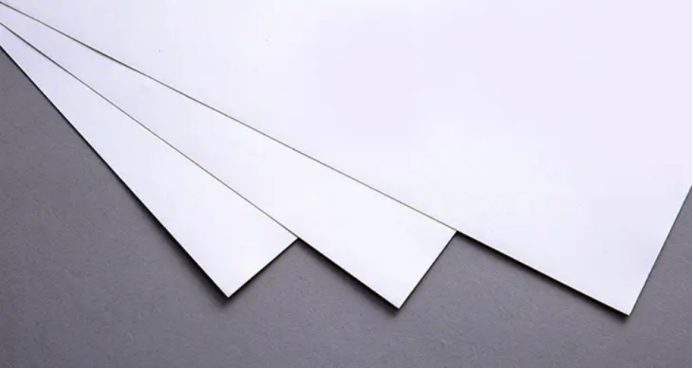
Art paper
Copperplate paper includes grey copper, white copper, single copper, fancy card, gold card, platinum card, silver card, laser card, etc.
“White bottom white board” refers to the white copper and single copper, which belong to the same type of paperboard.
“Double copper”: Both sides have coated surfaces, and both sides can be printed.
The similarities between white copper and double copper are that both sides are white. The difference is that the front side of white copper can be printed, while the back side cannot be printed, while both sides of double copper can be printed.
Generally, white cardboard, also known as “single powder card” paper or “single copper paper”, is used.

Gold cardboard
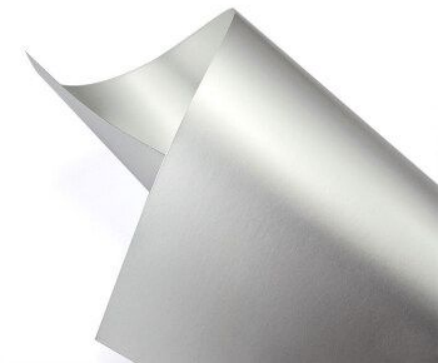
Silver cardboard
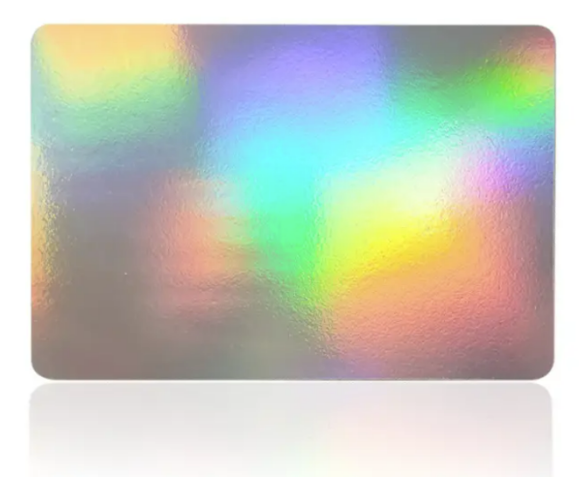
Laser cardboard
Grey board paper is divided into grey bottom grey board and grey bottom white board.
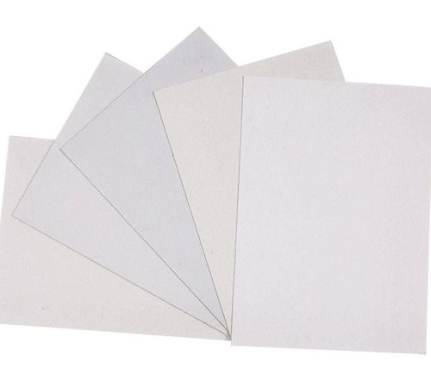
Grey board paper
Grey bottom grey board is not used in the packaging box printing and production industry.
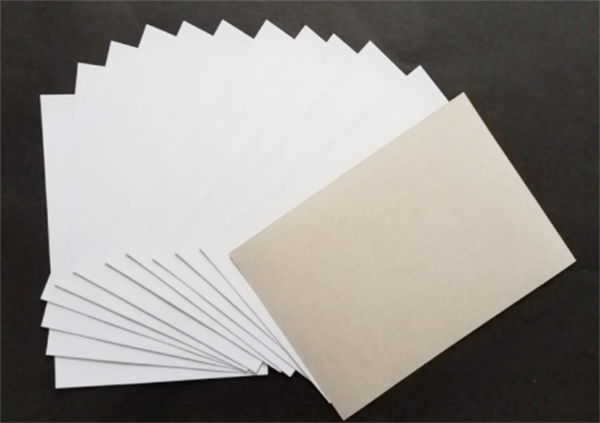
Grey bottom white board is also known as “powder grey paper, powder board paper”, with a white surface that can be printed and a grey surface that cannot be printed. It is also called “white board paper”, “grey card paper”, “single-sided white”. This kind of paper box has relatively low cost.
Generally, white cardboard, also known as “white bottom white board” paper or “double powder paper”, is used. White cardboard is of good quality, with a hard texture, and relatively expensive.
The packaging box material is determined by the shape and size of the product. The commonly used materials are: 280g powder grey paper, 300g powder grey paper, 350g powder grey paper, 250g powder grey E-pit, 250g double powder E-pit, etc.
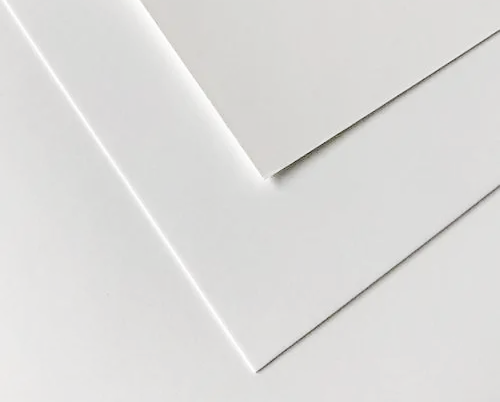
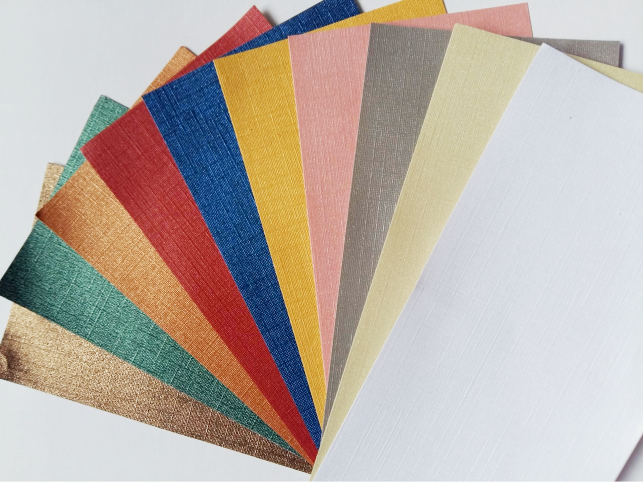
Specialty paper
There are many types of special paper, which are a general term for various special-purpose or art papers. These papers are specially treated to enhance the texture and level of packaging.
The embossed or embossed surface of special paper cannot be printed, only surface stamping, while star color, gold paper, etc. can be printed in four colors.
Common types of special paper include: leather paper series, velvet series, gift packaging series, bicolour pearl series, pearl paper series, bicolour glossy series, glossy series, packaging paper series, matte black card series, raw pulp color card series, red envelope paper series.
The surface treatment processes commonly used after surface paper printing include: gluing, UV coating, stamping, and embossing.
02
Corrugated Paper
Corrugated paper, also known as cardboard, is a combination of a flat kraft paper and a wavy paper core, which is more stiff and has a higher load-bearing capacity than ordinary paper, making it an important material for paper packaging.
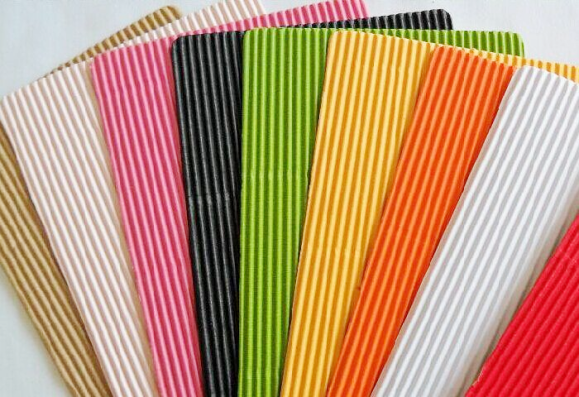
Colored corrugated paper
Corrugated paper is mainly used for outer packaging and comes in various styles, with commonly used types including three-layer (single-wall), five-layer (double-wall), seven-layer (triple-wall), and so on.
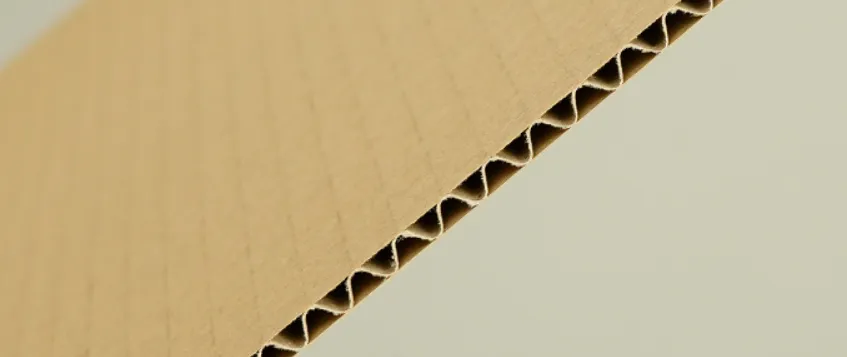
3-layer (single wall) corrugated board
5-layer (double wall) corrugated board
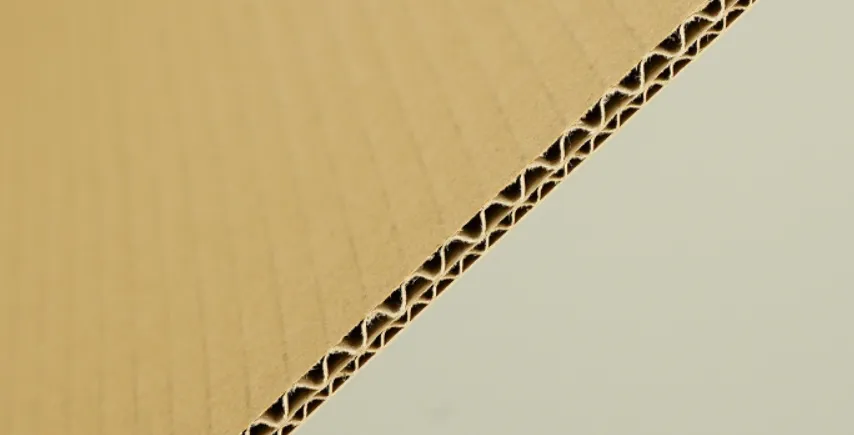
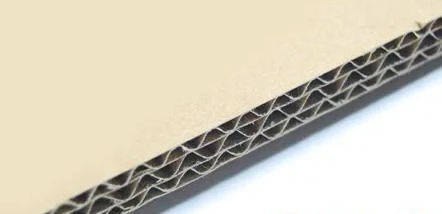
7-layer (triple wall) corrugated board
There are currently six types of corrugated paper: A, B, C, E, F, and G, but no D. The difference between E, F, and G corrugations is that they have finer waves, which maintain their strength while feeling less rough, and can be printed in various colors, but their effect is not as good as that of single-copper paper.
That's all for today's introduction. In the future, we will discuss common surface treatment processes used after printing, including gluing, UV coating, hot stamping, and embossing.
Post time: Mar-17-2023